The cost of regulatory compliance is substantial. According to the Competitive Enterprise Institute, large companies are reporting that the average cost of maintaining compliance is up to $10,000 per employee. Deloitte believes that financial institutions' expenses have climbed by more than 60% when compared to compliance expenditure levels prior to the financial downturn. Although rules are designed to protect against risk, they are becoming increasingly complex and expensive to comply with.
Figure 1: Number of rules for compliance across U.S. Industries
Source: https://xyleme.com/the-high-cost-of-regulatory-audits-non-compliance/
Despite the costs of compliance rising, research indicates that it is at minimum 2.7 times more expensive to not comply with requirements. That seems like a surprising number. But research from Ponemon and Globalscape shows that the average cost of compliance is $5.5 million, but the average cost of non-compliance is $15 million – nearly 3 times. Businesses usually assume that they cannot afford the necessary procedures and tools needed for enhanced compliance. However, this recent research from Ponemon and Globalscape reveals that failing to comply with standards is 2.7 times more expensive for a business. As former Assistant U.S. Attorney General Paul McNutty said, "If you think compliance is expensive try non-compliance". There are many tools and platforms available to manage quality control and compliance. They range from providing specialized solutions for specific industries to generic platforms that help across the enterprise.
So what are some of the ways to lower the cost of compliance?
-
- Avoiding quality/ compliance issues in processes in the first place. This can significantly reduce costs, as the amount of and even the cost of rework decreases significantly. Do it right the first time. The use of automated Quality control tools establishes a productive and efficient testing platform for any type of process, rather than checking the end product. That’s because surprises at the end are frequently pricey. Changes in the end product entail additional lost time, probably increased costs to fix, and much more.
For instance, one incorrect entry when manually entering data might result in a number of problems, particularly if the error goes undiscovered. However, cutting-edge compliance software like Copasys, an automated QC and compliance platform for multiple industries, can link data from multiple sources including documents using ICR/OCR, thereby reducing the chance of errors going through. Without this technology, manually entering data and conducting various checks to assure its accuracy would take far more time, and may be expensive, while still not assuring 100% accuracy. Automation of checking rules ensures consistency, high speed of testing, and a much lower cost per transaction by fixing issues at the place they occur.
- Avoiding quality/ compliance issues in processes in the first place. This can significantly reduce costs, as the amount of and even the cost of rework decreases significantly. Do it right the first time. The use of automated Quality control tools establishes a productive and efficient testing platform for any type of process, rather than checking the end product. That’s because surprises at the end are frequently pricey. Changes in the end product entail additional lost time, probably increased costs to fix, and much more.
Figure: Using input from documents and systems for automated QC, compliance, remediation, and reporting.
-
- Ability to use automated workflow to remediate issues to completion: Alongside employing an automated QC and compliance platform for issue detection, it’s advisable to find ways to remediate issues as soon as possible. If the remediation process is workflow-enabled, like in Copasys, it makes tracking of issues to completion more accurate and consistently faster. Even more importantly, this produces an audit trail of issues and fixes that is very useful for the next step below.
- Ability to fix issues not just for that cycle but fix defective processes. Effective compliance programs focus on more than just finding issues – we need to fix them permanently as well. It is important constantly analyze and anticipate any quality control and compliance issues. With in-depth insights into checking data for an underlying cause as well as impact assessment to identify flaws, an automated platform delivers quicker identification of major repetitive issues, and can even help with information at a granular level – even identify an agent that may be committing the same error, or a training issue across the department. Enterprises obtain actionable data to establish a Center of Excellence for Enterprise Risk when coupled with AI/ML competencies.
- Ability to automate and support regulatory reporting: Identifying what must be reported and when to be reported, and how it should be presented takes up a lot of effort in regulatory reporting. Automated solutions already have the quality control data based on analysis of transactions, and can use the pre-built configurable rules to determine reporting requirements, analyze it based on the precedent rules and circumstances, and output information to start an automated process that will access various company resources to create the reports.
- Ability to use automated workflow to remediate issues to completion: Alongside employing an automated QC and compliance platform for issue detection, it’s advisable to find ways to remediate issues as soon as possible. If the remediation process is workflow-enabled, like in Copasys, it makes tracking of issues to completion more accurate and consistently faster. Even more importantly, this produces an audit trail of issues and fixes that is very useful for the next step below.
Figure: Different aspects of QC, Compliance & Audit typically covered by automated platforms
What aspects help in managing QC, compliance, and in reducing costs?
Typical QC and compliance management and especially cost reduction is best addressed by addressing four important areas that feed into Compliance management:
- Data aggregation – especially if data needs to be collected from multiple sources, including documents
- Management of Rules – pre-built and/or user-defined rules that do the checking
- Workflow – to manage and document and resolve exceptions
- Reporting – with drill-down capability to allow for defect identification and resolution
A typical automated solution would be able to handle all these areas and more.
Figure: Snapshot of an automated QC, risk management, and regulatory compliance platform and services
To conclude, the cost of non-compliance is about three times more than that of the cost of compliance. So it is best to invest in a compliance solution that is sophisticated enough, and this in turn would quickly result in overall much lower costs in business operations, by reducing rework and even any financial impact of non-compliance.
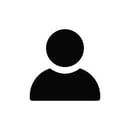
Explore Coforge's BPS success stories. Discover how we drive efficiency, innovation, and customer satisfaction across various industries.
Related reads.
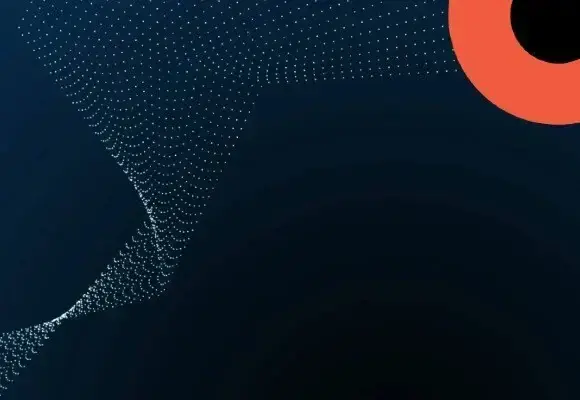
About Coforge.
We are a global digital services and solutions provider, who leverage emerging technologies and deep domain expertise to deliver real-world business impact for our clients. A focus on very select industries, a detailed understanding of the underlying processes of those industries, and partnerships with leading platforms provide us with a distinct perspective. We lead with our product engineering approach and leverage Cloud, Data, Integration, and Automation technologies to transform client businesses into intelligent, high-growth enterprises. Our proprietary platforms power critical business processes across our core verticals. We are located in 23 countries with 30 delivery centers across nine countries.